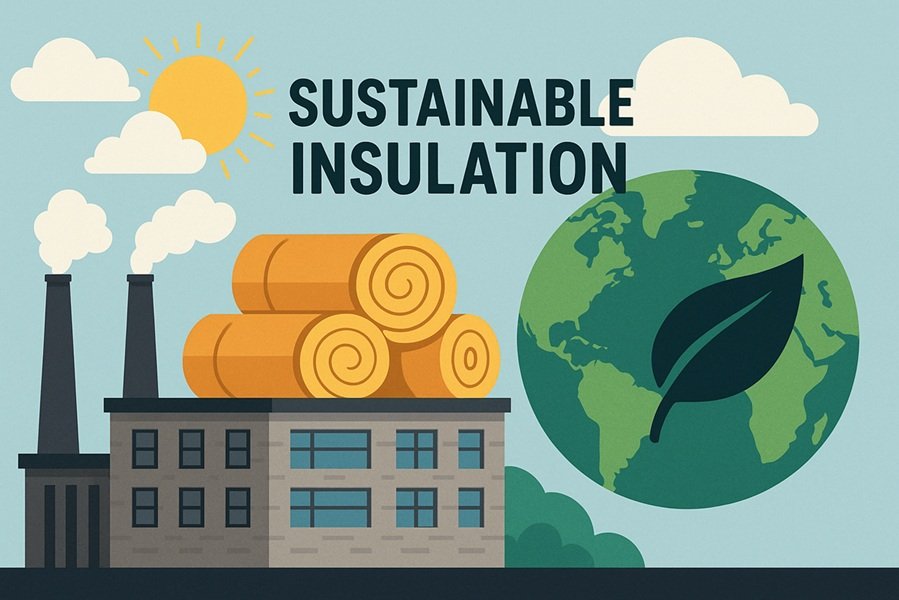
Greener by Design: The Business Case for Sustainable Insulation Materials
As the global climate conversation accelerates, insulation materials—often overlooked in sustainability discussions—are gaining critical importance. With buildings and industrial operations accounting for nearly 40% of global carbon emissions, energy-efficient insulation has emerged as a key driver for both environmental performance and long-term operational efficiency.
In this evolving landscape, industry leaders like PBM Insulations are helping reshape the standards by investing in research, responsible materials, and engineering processes that align thermal performance with environmental impact.
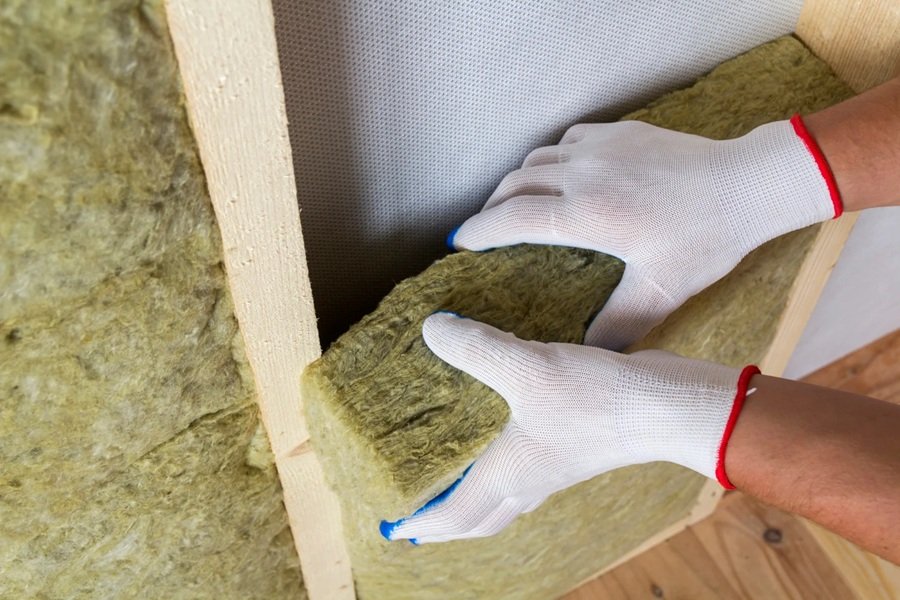
Insulation isn’t just about heat resistance anymore. It’s about how manufacturers and OEMs can align with evolving environmental standards, deliver cost savings, and meet growing market expectations—all without compromising performance.
Rethinking Insulation in a Net-Zero World
Governments and industries are pushing for carbon neutrality. Green building codes, ESG regulations, and climate-conscious procurement are prompting businesses to reassess material choices. For insulation, this means a move away from energy-intensive, non-recyclable materials towards bio-soluble fibers, recycled content, and lightweight composites.
Sustainable insulation contributes in multiple ways:
- Reduces energy demand for heating and cooling
- Enhances indoor air quality and fire safety
- Lowers lifecycle emissions of industrial and mobile assets
To stay competitive and compliant, manufacturers are increasingly tracking insulation industry trends. From fire-safety innovations to aerogel-based EV applications—to guide future investments and product development.
Economic Value Beyond the Environment
Sustainability is not just an ethical imperative—it’s a business advantage. Several economic factors make a compelling case for the adoption of eco-conscious insulation solutions:
1. Energy Efficiency = Cost Efficiency
High-performance insulation reduces heat loss and improves operational efficiency in HVAC systems, machinery, and vehicle cabins. Over time, this leads to significant energy savings—an increasingly important factor as fuel and electricity costs rise globally.
2. Durability Reduces Maintenance
Many sustainable insulation materials—like aerogels or glass fiber composites—offer longer service life, resistance to corrosion, and greater structural integrity. This translates to fewer replacements and reduced downtime across industrial operations.
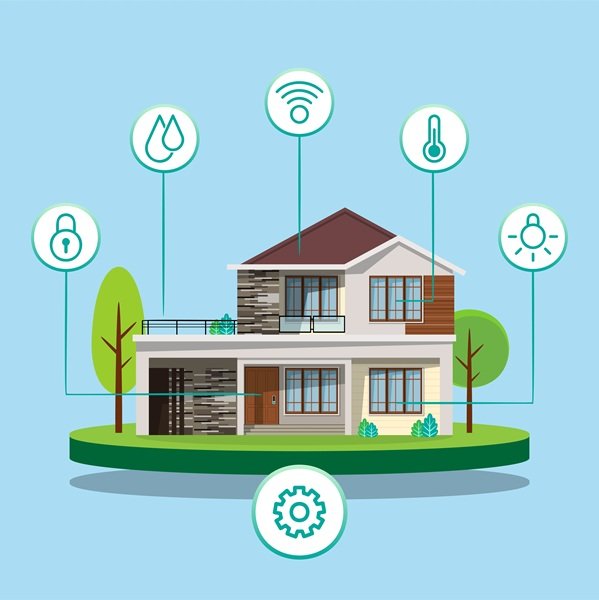
3. Fulfilling ESG Mandates
With ESG metrics becoming central to investment decisions and supply chain approvals, using greener materials can improve a manufacturer’s environmental footprint, helping them meet client, investor, and regulatory expectations more confidently.
What Makes Insulation ‘Sustainable’?
Not all insulation labeled as “eco-friendly” delivers the same outcomes. Truly sustainable insulation balances material science, design precision, and life cycle performance.
Here are some key parameters:
- Thermal Conductivity: Efficient insulation minimizes energy loss.
- Fire Safety: Non-toxic, fire-resistant materials reduce risk in high-temperature applications.
- Recyclability & Bio-Solubility: Materials that break down safely or are derived from recycled inputs reduce environmental load.
- Manufacturing Footprint: Cleaner production methods with minimal VOC emissions, waste, or water usage support larger sustainability goals.
Designing for the Future: EVs and Electrification
With electric vehicles (EVs) transforming mobility, insulation is playing a new role. EV batteries demand insulation that is:
- Lightweight and space-efficient
- Capable of withstanding thermal shock and high voltage zones
- Non-conductive and flame retardant
Advanced solutions like aerogel mats, C-glass fiber wraps, and foil-laminated slabs are now being explored for their ability to protect battery enclosures, improve vehicle range, and maintain thermal stability under extreme conditions.
Beyond automotive, the same materials are being considered in energy-intensive areas such as data centers, power systems, and defense applications.
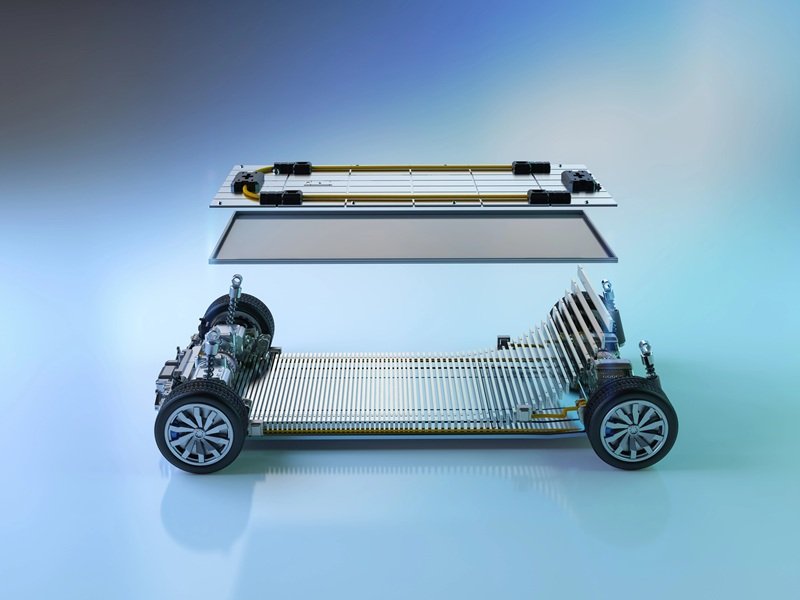
The Supply Chain Advantage: Compliance + Credibility
Insulation manufacturers today are increasingly expected to demonstrate adherence to global standards like:
- ISO and IATF certifications for quality and manufacturing
- Ecovadis ratings for sustainability transparency
- Zero-child-labour and ethical sourcing policies
For OEMs and contractors, working with insulation suppliers who meet these benchmarks reduces risk exposure and enhances their own compliance narrative.
In this context, sustainability isn’t just a function of the product—it’s embedded in the systems, certifications, and processes that surround it.
The Role of R&D in Material Transition
The future of insulation depends not just on current offerings, but on how companies are investing in R&D and testing protocols to drive material evolution. Simulation tools like thermal modeling software now allow engineers to test material performance under real-world stress scenarios before production, significantly reducing development cycles.
Thermal testing setups like muffle furnaces, shrinkage analyzers, and moisture content ovens are becoming standard in in-house labs, enabling real-time validation of insulation behavior in demanding environments.
Data-led decision making around material choice, thickness optimization, and fire behavior is a growing differentiator for insulation providers that support high-precision industries like EVs, defense, and industrial automation.
What Manufacturers Should Keep in Mind
For manufacturers evaluating insulation suppliers or planning their next production line, here are four takeaways:
- Don’t Just Look at Cost per Square Meter. Evaluate total cost of ownership—how much energy the insulation will save, how often it needs to be replaced, and how it aligns with your ESG goals.
- Assess the Life Cycle Impact. Ask for details about the material’s origin, recyclability, and what happens at the end of its life. Recycled or bio-soluble options are increasingly available and effective.
- Verify Standards and Certifications. Ensure your insulation partner complies with international quality and environmental benchmarks. Certifications aren’t just checkboxes—they build trust throughout your value chain.
- Think Platform-Specific. Different applications demand different solutions. Thermal shields for EV batteries, for instance, must be light and non-conductive—entirely different from insulation used in boilers or turbines. Customization capability matters.
Conclusion: A New Insulation Mindset
As the demand for sustainable infrastructure and clean mobility rises, insulation is being reimagined—not just as a passive material but as an enabler of performance, safety, and responsibility. The next generation of insulation will not only meet thermal demands but also tick boxes for durability, compliance, and climate impact.
Forward-thinking manufacturers are already making the shift—viewing insulation not just as a spec to meet, but a strategy to lead.